Over the summer of 2015 I was fortunate to spend some time with Laing O’Rourke, the international engineering company whose projects have included the London 2012 Olympic Stadium, ‘the Cheesegrater‘ (a skyscraper in the City of London), and Heathrow Terminal 5. The current focus while I was there was Crossrail, the largest construction project in Europe at the time, consisting of 73 miles of railway lines with 42 stations, beneath the streets of London. The trains in question will be 200m long and able to carry 1,800 passengers. Construction began in 2009 after decades of planning and should be completely finished in 2019, with the central section of the route to open in late 2018. The cost of this immense project is around £15 billion (see BBC 2‘s documentary ‘The Fifteen Billion Pound Railway’ from 2014-15).
As Laing O’Rourke is such a large company (over 15,300 employees), there are very few subcontractors for the Crossrail project, but specialist knowledge is needed for aspects like tunnelling, involving eight tunnel boring machines, and so this was subcontracted.*
My first day started off with a tour of the Broadgate Ticket Hall at Liverpool Street Station in London, and I was surprised by the sheer number of safety procedure and warning signs that were dotted all around the site. In the canteen I later found a whole wall dedicated to Health and Safety, including a count of days with no serious injuries on site and a diagram showing where most accidents occur (hands and feet). I saw where the escalator will be situated, with the glass roof descending at a 30 degree angle above the escalator’s 16 degree slant from the ground. Some of the permanent-looking steel girder structures around Broadgate Ticket Hall I found to be only temporary; constructed to support the weights of the two massive cranes on site.
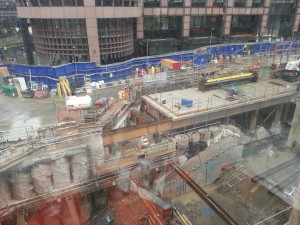
An area hidden by a tents was in fact the MOLA (Museum of London Archaeology) excavation site that was the focus of much news in the UK after a mass burial ground was discovered once digging for Crossrail began. Although this did delay Crossrail, the Bedlam Burial Ground – which dates back to about the fifteenth century – has been a valuable find for those interested in the history of London. Due to a shortage of burial space during the Great Plague of 1665, rich and poor alike were buried together from a hospital nearby, quite unusual for the time. Some skeletons were found with a sort of rust on their ribcage and these were understood to be the remains of richer citizens, whose wooden coffins had deteriorated to leave the metal nameplates on the top to be pressed together with the bones.
Throughout my time at Laing O’Rourke I used an EDM (Electronic Distance Measurement) device on multiple occasions, calibrating the device with various targets dotted around on nearby buildings so that the machine would know exactly where in the site measurements were being taken from. A slight wobble or too harsh a press of a button can cause the EDM to lose it’s position, and it has to be re-calibrated – a process I began to find rather time-consuming after I had jolted the EDM a fair number of times! I was allowed to measure the positions of piles within the site, and then by uploading the data later in the office, I could compare the theoretical positions to the actual positions of the piles on AutoCAD. I drew circles-of-best-fit using the three points I had measured on each pile and as long as there wasn’t a difference of more than 20mm, there wasn’t an issue. I later also used the EDM to take measurements on the MOLA site and uploaded this to AutoCAD to draw a contoured map of the area.
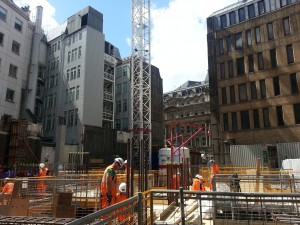
I also entered the Blomfield Box site, just a building over from Broadgate Ticket Hall, dedicated to building the maintenance aspects of the station, and not anticipating having any people walking through. I got to check that there were 28 fastenings around all main concrete reinforcements, suitably distanced apart, which was one of the many requirements from the structural engineers who had drawn up the plans. Structural engineers always “over-design” because they know designs will be compromised, either through necessity or construction teams taking shortcuts. Although everyone knows this on site, they still need to build as close to the plans as possible, so when we found a distance between the fastenings to be too wide, the engineer on site knew it would have to be re-fitted for inspection although it would clearly never cause an issue. The site was right next to a London underground line, and a higher screen needed to be built so that debris didn’t fall onto the tracks. This had to be done on the night shift between 01:00 and 05:00, because that was the only time trains wouldn’t be passing by.
The Moorgate Ticket Hall is another of the many Crossrail stations and will be connected by an underground walkway to the Liverpool Street site. Crossrail has been so long in the planning that Moor House (a building right next to Moorgate station) was built with a basement and vent for relieving air pressure from Crossrail trains, but when Crossrail began work, they found the basement full of clothing racks because a fashion retailer situated in Moor House thought it an ideal storage area! An interesting engineering aspect of Moorgate Ticket Hall was that some of the columns were being made by filling a mold with concrete and then inserting the reinforcements. Another thing I learnt when I asked why there were many small sets of steps and an elevator situated next to each instead of just an inclined floor, was how strict rules are for ramps for wheelchairs and that there wasn’t enough space around the corners to safely have a ramp beneath the maximum angle. Another factor of the Moorgate Ticket Hall was that two long beams (≈17m) are to go through the ticket hall, but lorries are limited to 12m, so two sets of pairs of beams would need to be spliced. After looking down at the disconcertingly large hole in the ground with many buildings still standing right around the rim, I was also allowed into the old Moorgate underground station, which is now being partially torn down, with Asbestos removal in progress. It was rather eerie walking through the half-lit empty station where walls had been ripped away and ticket barriers were missing, seeing as I had often used the station before it closed. After that morning on-site I went through drawings of trusses, orthographic projections, and instructions for construction, all of which the engineer I was with, had to check through and approve. I was really impressed by how quickly she picked up discrepancies on pages that were so cluttered with hundreds of dimensions.
Something more on my level was going back into the Broadgate site to measure the depth of the pit (which had noticeably increased even after the few days I had been present and was now at 15m), and spray markings on the wall so that the diggers knew how much further to pit out the piles. Another practical job was to put up more targets for EDM positioning mentioned earlier, using a resin gun that dried out all too quickly. I attended one of Crossrail’s regularly held “Tool Box Talks”, covering innovation on-site and measuring individual site creativity. One team used a projector for task briefings on-site, saving an hour per briefing from not needing to walk from the site to the offices and back to the site. I tried out “Google Cardboard” with the “Photosphere” app to view a 360˚ projection of the Broadgate site, which is useful in offices so that people don’t always need to go onto site to check minor things.
I learnt a great deal in my short time at Laing O’Rourke, not least about what it is like to be an engineer. I had come in thinking that individuals would focus on single elements of projects, but there’s a holistic approach as engineers in meetings discussed all the various events taking place at Liverpool Street, from deliveries to how a particular construction area is going. The engineers were also on site much more than I had thought and constantly going in and out of the office – meaning that everyone wears their PPE (Personal Protective Equipment) throughout the whole day and I was sad to part with my neon orange salopettes. The engineers on Crossrail had much more varied working hours than I had anticipated; I’d walk in just before nine to find most engineers already working since seven and ready to take their first break. Working for a contractor tends to involve longer hours than working for clients directly, it seemed. And I needed to remind myself that as enjoyable as it was walking on site to take measurements while enjoying some (relatively) fresh air, I’d probably not quite be so keen to need to gear up in December frost. All in all, this work experience really showed me what I can anticipate as an engineer working on-site and I can’t wait to step onto the Crossrail trains in 2018 and excitedly tell everyone the facts and figures I know.
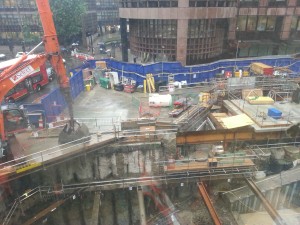
* Some months after my Crossrail experience, I attended a talk by employees of Dragados Sisk, who were the tunnelling subcontractors, and it was interesting to hear about the tunnelling process (at Laing O’Rourke the focus had nearly solely been on stations and ticket halls), especially how they assembled and disassembled the boring machines within the tunnels and how they found some extremely strong Victorian brick tunnels, that they needed to partially tear down.